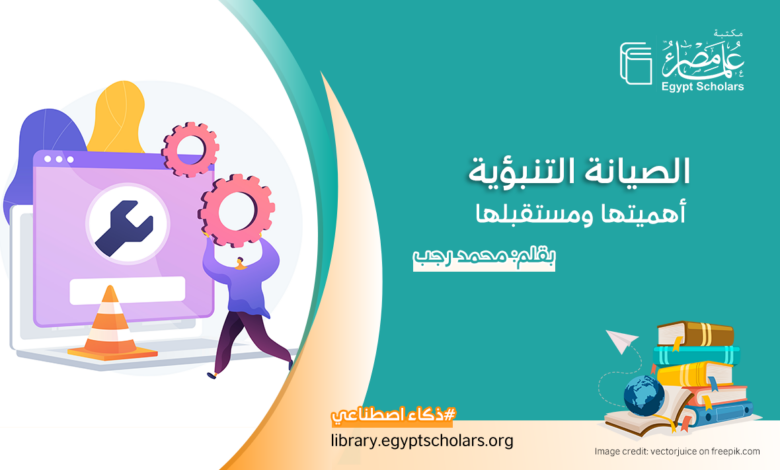
الصيانة التنبؤية
أهميتها و مستقبلها
في حياتنا اليومية، نعتمد بكثرة على الآلات الصناعية المتواجدة في القطارات، الطائرات، السفن، والمصانع، وغيرها من مجالات الصناعة. الحقيقة المؤكدة أنه لا توجد آلة تعمل إلى الأبد دون أن تتعرض للتوقف، إلا أن «التوقف غير المخطط له» (Unplanned Downtime) يمكن أن يتسبب في عواقب هائلة من عدة جوانب:
أولًا: من ناحية الأمان؛ حيث يمكن أن يؤدي تعطل بعض الآلات والمحركات إلى إصابات بالغة للعاملين، قد تصل حتى إلى خسائر بشرية، خاصةً في قطاع الطيران.
ثانيًا: من ناحية الخسائر المادية؛ ففي بعض الصناعات، تكون تكلفة التوقف لإصلاح الأعطال ضخمة جدًا. على سبيل المثال: تصل تكلفة التوقف لمدة ساعة واحدة فقط في «صناعة السلع الاستهلاكية» (Fast-moving Consumer Goods) إلى 36000 دولار، وتزيد إلى 30000 دولار في الساعة في «الصناعات الثقيلة» (Heavy Industries)، ويمكن أن تصل إلى 2.3 مليون دولار في الساعة (أي 600 دولار في الثانية) في «صناعة السيارات» (Automotive Industry). كما أن إجمالي تكلفة التوقف غير المخطط له في أكبر 500 شركة في العالم يصل إلى 11% من الربح الكلي للشركات، بما يعادل 1.4 تريليون دولار، وهو ما يعادل الناتج المحلي الإجمالي لدولة مثل إسبانيا. يمكنكم مراجعة تقرير شركة سيمنز لعام 2024 عن التكلفة الحقيقية للتوقف غير المخطط له [1].
إذًا، ما السبيل لحل هذه المشكلة؟
الصيانة هي الحل الرئيسي لتقليل هذه التكلفة الضخمة. وهناك عدة طرق للصيانة:
1. «الصيانة التصحيحية» (Reactive Maintenance or Corrective Maintenance): هذا النوع التقليدي يعتمد على استخدام الآلة حتى تعطلها ثم استبدال الجزء المعطوب. ورغم بساطة هذه الطريقة وانخفاض تكلفتها، إلا أنها غير قابلة للتطبيق في كل المجالات، فقد تتسبب بعض الأعطال في خسائر بشرية ومادية ضخمة. مثلًا: حال حدوث عطل في توربينات الرياح، يصعب تغيير هذه التوربينات، وتكون التكلفة كبيرة، وقد تكون خطرًا مهددًا لحياة العاملين بها.
2. «الصيانة الوقائية» (Preventive Maintenance): تُعتبر هذه الطريقة الأكثر انتشارًا حاليًا، حيث تُجرى الصيانة دوريًا لمنع حدوث التوقف غير المخطط له. ورغم فاعلية هذه الطريقة في تقليل التوقفات غير المخطط لها، إلا أنها لا تساعد في تقليل فترات التوقف، حيث يتم إيقاف الماكينة أو المصنع عند إجراء الصيانة الدورية. بالإضافة إلى ذلك، نظرًا لأن الصيانة لا تأخذ في الحسبان حالة القِطَع التي يتم استبدالها؛ قد تُستبدل بعض القطع التي لا تزال صالحة للعمل، مما يزيد في التكلفة نتيجة عدم الاستخدام الأمثل للقطع المستبدلة.
3. «الصيانة التنبؤية» (Predictive Maintenance): تُعتبر هذه الطريقة حلًا لمشاكل الطرق السابقة بهدف تقليل فترات التوقف والسماح بالاستخدام المثالي للماكينات والآلات. حيث تتم في الصيانة التنبؤية «متابعة حالة الآلات» (Machine Health Monitoring) والتنبؤ بالتوقيت المتوقع لتعطل الآلات بناءً على حالتها اليومية. وبذلك، تُجدول الصيانة وفقًا لحالة الآلات، وتُستخدم القطع حتى آخر عمرها/ ثم تُستبدل قبل فترة قصيرة من تعطلها. هذه الطريقة أفضل بمراحل من الصيانة الدورية، حيث تطول الفترة بين الصيانات، وتُستخدم والقطع والآلات بكفاءة أكبر.
دور الذكاء الاصطناعي في تحقيق الصيانة التنبؤية
باستخدام «البيانات الضخمة» (Big Data) و«التحليلات المتقدمة» (Advanced Analytics)، يلعب «الذكاء الاصطناعي» (AI) دورًا محوريًا في تحقيق الصيانة التنبؤية [2]. وتتكون العملية من عدة خطوات متسلسلة ومترابطة:
- «مراقبة حالة الآلة» (Condition Monitoring): تبدأ العملية بمتابعة حالة الآلة تلقائيًا باستمرار، مما يسمح بالكشف المبكر عن أي تغيرات قد تؤدي إلى مشكلات في المستقبل.
- «تحديد الأنماط التي تشير إلى أعطال محتملة» (Anomaly Detection): بعد مراقبة حالة الآلة، يُستخدم الذكاء الاصطناعي لتحديد العلامات المبكرة التي تشير إلى وجود خلل محتمل، مما يمكّن الشركات من تجنب هذه الأعطال قبل وقوعها.
- «التنبؤ المبكر بتوقيت العطل المتوقع» (Fault Prognosis): هذه الخطوة تستفيد من البيانات والأنماط المحددة لتوقع وقت وقوع العطل، مما يساعد الشركات على الاستعداد لأي توقفات والتخطيط لها بفعالية أكبر.
- «تحديد مكان العطل بدقة» (Fault Diagnosis): في حال حدوث العطل، يعمل الذكاء الاصطناعي على تحديد مكان العطل بدقة، مما يسرع من عملية تجهيز وتوفير قطع الغيار اللازمة من سلاسل الإمداد ويقلل من وقت التوقف التام للآلات.
مستقبل الصيانة التنبؤية
مع تزايد تطبيقات الصيانة التنبؤية في الصناعات المختلفة، لا تزال هناك تحديات كثيرة لتنفيذ هذه المهام بدقة. ومع ذلك، بدأت بعض الصناعات بالفعل في استخدام الصيانة التنبؤية، واستطاعت تحقيق نتائج ملحوظة، حيث تمكنت من تقليل معدل التوقف بنسبة 50% وخفض تكاليف الصيانة بنسبة 40%. هذه الإنجازات ليست نقلة نوعية في كيفية صيانة المعدات فحسب، بل تمثل ثورة حقيقية تقود القطاعات الصناعية نحو عالم تقل فيه تكاليف الصيانة بملايين الدولارات، وتصبح الأعطال الكبيرة جزءًا من الماضي.
وعلى المستوى العالمي، من المتوقع أن تحقق صناعة الصيانة التنبؤية إيرادات تصل إلى حوالي 60.126 مليار دولار بحلول عام 2030، مع معدل نمو سنوي مركب يبلغ 29.5% من عام 2024 حتى 2030. هذه الأرقام تعكس الإمكانيات الهائلة للصيانة التنبؤية وتؤكد على أهميتها كعنصر أساسي في تعزيز الكفاءة وخفض التكاليف في الصناعات الحديثة [3].
في مقال قادم:
سنبدأ في التعرف بطريقة أكثر تفصيلًا على خطوات تطبيق الذكاء الاصطناعي و«التعلم من البيانات» (Data-driven Models) في الصيانة.
المصادر
[1]- Siemens Annual Report on the True Cost of Unplanned Downtime. View the report.
[2]- Daily, Jim, and Peterson, Jeff. “Predictive Maintenance: How Big Data Analysis Can Improve Maintenance.” In Supply Chain Integration Challenges in Commercial Aerospace: A Comprehensive Perspective on the Aviation Value Chain, (2017): 267-278.
[3]- Global Market Size for Predictive Maintenance. View the study.